نحوه کارکرد دستگاه تراشکاری cnc
دستگاه لَته CNC (Computer Numerical Control) به عنوان یکی از پیشرفته ترین ابزارهای صنعتی، نقشی اساسی در فرآیند تراشکاری cnc و تولید قطعات با دقت بالا ایفا می کند. اهمیت این دستگاه در دنیای امروز به دلیل توانایی آن در خودکارسازی فرآیندهای تولید و کاهش نیاز به نیروی کار ماهر، به وضوح نمایان است. این دستگاه با دریافت دستورالعمل های کدگذاری شده از نرم افزارهای مخصوص، قادر به انجام عملیات برش و شکل دهی به قطعات مختلف می باشد. اجزای اصلی لَته CNC شامل بدنه ماشین، محور اصلی، چاک و ابزار برش است که هر یک وظیفه ای خاص در فرآیند تولید دارند. با استفاده از چندین محور، این دستگاه می تواند اشکال پیچیده ای را با دقت بالا تولید کند. در این مقاله به بررسی نحوه کارکرد این دستگاه و فرآیندهای اجرایی آن خواهیم پرداخت که نشان دهنده تأثیر شگرف فناوری در صنایع تولیدی است.
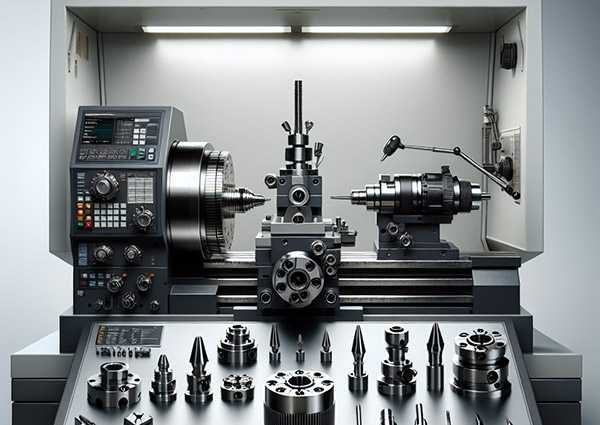
اجزای اصلی دستگاه تراشکاری CNC
بدنه ماشین CNC لته به عنوان پایه و چاسیس دستگاه، از اهمیت بالایی برخوردار است. این قسمت باید به گونه ای طراحی شود که بتواند بارهای سنگین و لرزش های ناشی از عملیات ماشین کاری را به خوبی تحمل کند. برای این منظور، معمولاً از مواد مقاوم مانند چدن یا فولاد استفاده می شود. این انتخاب مواد نه تنها باعث افزایش دوام و طول عمر دستگاه می شود، بلکه کیفیت کار نهایی را نیز تحت تأثیر قرار می دهد. بدنه باید دارای طراحی مناسب و متناسب با ابعاد و ظرفیت دستگاه باشد تا موجب ایجاد ثبات و دقت در طول فرآیند ماشین کاری گردد.
محور اصلی
محور اصلی یا headstock، یکی از اجزای حیاتی دستگاه لته است که نیروی محرکه را تأمین می کند و وظیفه نگهداری قطعه کار را بر عهده دارد. این بخش شامل یک موتور قدرتمند و بلبرینگ هایی است که به تحمل بارهای سنگین کمک می کنند. قدرت موتور و ابعاد headstock به طور مستقیم بر ظرفیت کار دستگاه تأثیر دارند. به عبارت دیگر، هر چه موتور قوی تر باشد، دستگاه قادر به انجام عملیات پیچیده تر و با دقت بیشتری خواهد بود. این قسمت در واقع قلب تپنده دستگاه است و عملکرد صحیح آن برای کیفیت و دقت برش بسیار ضروری است.
چاک
چاک (chuck) یکی از اجزای کلیدی در دستگاه لته CNC به شمار می آید که وظیفه نگه داشتن قطعه کار را در مرکز دوران بر عهده دارد. انواع مختلفی از چاک ها وجود دارند که شامل:
- چاک های سه فک
- چاک های چهارفک
- چاک های مغناطیسی
انتخاب نوع چاک مناسب بستگی به نوع عملیات و شکل قطعه کار دارد. به عنوان مثال، چاک های سه فک برای قطعات گرد و چاک های چهارفک برای قطعات غیر گرد مناسب تر هستند. دقت در انتخاب چاک می تواند تأثیر زیادی بر روی کیفیت برش و کارایی فرآیند ماشین کاری داشته باشد.
ابزار برش
ابزار برش (cutting tools) نیز از اجزای کلیدی دستگاه لته CNC محسوب می شود که وظیفه اصلی آنها انجام عملیات برش و شکل دهی بر روی قطعه کار است. این ابزارها می توانند بسته به نوع عملیات و جنس مواد متفاوت باشند. ابزارهای برش شامل موارد زیر می شوند:
- ابزارهای کاربیدی
- ابزارهای سرامیکی
- ابزارهای الماسه
استفاده از ابزارهای با کیفیت و مناسب نه تنها به بهبود کیفیت نهایی قطعات تولیدی کمک می کند، بلکه می تواند موجب افزایش بهره وری و کاهش زمان تولید نیز گردد. انتخاب صحیح ابزار برش به فرآیند ماشین کاری کمک کرده و تأثیر مستقیمی بر روی هزینه ها و زمان تولید خواهد داشت.
نحوه دریافت و پردازش دستورالعمل های کدگذاری شده
برای پردازش دستورالعمل های کدگذاری شده در دستگاه های CNC، استفاده از نرم افزارهای مخصوص ضروری است. این نرم افزارها به عنوان پل ارتباطی میان اپراتور و دستگاه عمل کرده و امکان وارد کردن و ویرایش کدهای G و M را فراهم می آورند. با استفاده از این نرم افزارها، اپراتورها می توانند به سادگی تغییرات لازم را اعمال کرده و به راحتی فرآیند تولید را کنترل کنند.
ویژگی های کلیدی این نرم افزارها شامل:
– **رابط کاربری گرافیکی (GUI)**: این رابط کاربری به اپراتورها اجازه می دهد تا با بصیرت بیشتری با داده ها و کدها کار کنند.
– **جمع آوری داده ها**: نرم افزارها توانایی جمع آوری داده ها از دستگاه های مختلف و نمایش آن ها به صورت گرافیکی را دارند که به تحلیل دقیق تر فرآیند تولید کمک می کند.
– **تحلیل و بهبود**: با تجزیه و تحلیل داده های دریافتی، اپراتور می تواند نقاط ضعف و قوت فرآیند تولید را شناسایی کرده و به بهبود مستمر آن بپردازد.
کدهای G و M
کدهای G و M ابزارهای اصلی در زبان برنامه نویسی دستگاه های CNC هستند. کدهای G وظیفه تعیین مسیرهای حرکتی ماشین را بر عهده دارند و معمولاً شامل دستورات مربوط به برش و جابه جایی ابزار هستند. به عنوان مثال، کد G01 برای حرکت خطی و کد G02 برای حرکت دایره ای استفاده می شود.
از سوی دیگر، کدهای M به کنترل وظایف خاصی در دستگاه های CNC کمک می کنند. به عنوان مثال، کد M03 برای روشن کردن ابزار و کد M05 برای خاموش کردن آن به کار می رود. این کدها به اپراتورها اجازه می دهند تا عملکردهای جانبی دستگاه را مدیریت کنند و در نتیجه فرآیند تولید را بهینه سازی کنند.
انتقال داده ها به دستگاه
انتقال داده ها به دستگاه های CNC از طریق پروتکل های مختلف ورودی/خروجی (I/O) انجام می شود. این پروتکل ها شامل درگاه های موازی و سریال هستند که ارتباط بین کامپیوتر و دستگاه های خارجی را تسهیل می کنند. برای اینکه این انتقال به درستی انجام شود، کنترلرها نقش حیاتی دارند. آن ها باید اطمینان حاصل کنند که داده ها به درستی و بدون اختلال به اجزای مختلف دستگاه منتقل می شوند.
نکات کلیدی در انتقال داده ها:
– **کارایی و سرعت**: انتقال داده ها باید به گونه ای انجام شود که کارایی و سرعت پردازش را به حداکثر برساند.
– **پیشگیری از اختلال**: هرگونه اختلال در این فرآیند می تواند به کاهش کیفیت تولید و افزایش زمان تحویل منجر شود.
– **تنظیمات دقیق**: باید تنظیمات لازم روی پروتکل های I/O انجام شود تا اطمینان حاصل شود که داده ها به درستی پردازش می شوند.
با رعایت این نکات و استفاده از نرم افزارهای تخصصی، اپراتور می تواند به بهینه سازی فرآیند تولید در دستگاه های CNC بپردازد و کیفیت نهایی محصولات را افزایش دهد.
فرآیند تراشکاری با دستگاه CNC
تنظیم صحیح قطعه کار در دستگاه CNC یکی از مراحل حیاتی در فرآیند تراشکاری است. در این مرحله، قطعه کار باید به گونه ای در محل خود قرار گیرد که از هرگونه حرکت ناخواسته جلوگیری شود. این کار معمولاً با استفاده از گیره ها یا نظام های مخصوص انجام می شود. اطمینان از محکم بودن قطعه کار و قرارگیری صحیح آن در مرکز دستگاه، می تواند تأثیر بسزایی در دقت برش و کیفیت نهایی محصول داشته باشد. هر گونه نقص در این مرحله ممکن است منجر به تولید قطعات معیوب و افزایش هزینه های اضافی شود.
انتخاب ابزار مناسب
انتخاب ابزار مناسب برای تراشکاری با دستگاه CNC، عاملی کلیدی در بهبود کیفیت و کارایی تولید است. ابزارها باید با دقت انتخاب شوند تا متناسب با نوع ماده و نوع برش مورد نیاز باشند. به عنوان مثال، ابزارهای کاربیدی برای برش فلزات سخت و ابزارهای الماسه برای مواد نرم تر مناسب هستند.
در نظر گرفتن ویژگی های مواد: سختی، چقرمگی و نوع ماده می تواند در انتخاب ابزار تأثیرگذار باشد.
سرعت برش و عمق برش نیز باید با توجه به نوع ابزار انتخاب شده تنظیم شود.
شناخت دقیق از نیازهای پروژه و شرایط کاری می تواند به انتخاب بهینه ابزار کمک کند و در نتیجه زمان و هزینه تولید را کاهش دهد.
برش و شکل دهی
در این مرحله، دستگاه CNC بر اساس برنامه های از پیش تعیین شده، عملیات برش را آغاز می کند. این برنامه ها شامل پارامترهایی همچون سرعت برش، عمق برش و نوع حرکت ابزار است. دقت در اجرای این مراحل حیاتی است، زیرا هر اشتباه در اینجا ممکن است منجر به عدم تطابق قطعه نهایی با مشخصات مورد نظر شود.
استفاده از نرم افزارهای پیشرفته و تکنیک های کنترل کیفیت در این مرحله می تواند به بهبود فرآیند کمک کند. همچنین، انجام آزمایش های دوره ای بر روی قطعه های تولید شده می تواند به شناسایی مشکلات و بهبود کیفیت نهایی منجر شود.
کنترل دقت و کیفیت
کنترل دقت و کیفیت در فرآیند تراشکاری با CNC از اهمیت ویژه ای برخوردار است. برای اطمینان از اینکه قطعات تولید شده مطابق با استانداردهای لازم هستند، بازرسی های منظم و استفاده از نرم افزارهای کنترل کیفیت ضروری است. این بازرسی ها می توانند شامل بررسی ابعاد، شکل و سطح قطعه ها باشند.
اقدامات پیشنهادی برای بهبود کنترل کیفیت:
آموزش کارکنان در زمینه استانداردهای کنترل کیفیت و استفاده صحیح از ابزارهای بازرسی.
استفاده از سیستم های اتوماسیون برای کاهش خطاهای انسانی.
بررسی منظم و به روزرسانی تجهیزات و ابزارها.
این فرآیندها در نهایت به افزایش دقت و کاهش خطاها کمک کرده و به بهبود کیفیت نهایی قطعات تولیدی منجر می شود.
نحوه به کارگیری چندین محور در دستگاه CNC
دستگاه های CNC چندمحوره با استفاده از محورهای X و Z، امکان حرکت دقیق و کنترل شده ابزار و قطعه کار را فراهم می کنند. محور X معمولاً به عنوان محور افقی شناخته می شود و برای حرکت ابزار یا قطعه کار در راستای افق کاربرد دارد. در حالی که محور Z، معمولاً به عنوان محور عمودی عمل می کند و به حرکت عمودی ابزار یا قطعه کمک می کند. این دو محور اصلی، پایه ای برای انجام عملیات ماشین کاری فراهم می آورند و در ترکیب با سایر محورهای چرخشی، پیچیدگی های بیشتری را امکان پذیر می سازند.
استفاده از این محورهای پایه، به تولیدکنندگان این امکان را می دهد که قطعاتی با دقت بالا و سطوح صاف تولید کنند. به علاوه، این محورها در دستگاه های CNC قادر به انجام عملیات مختلفی مانند برش، خنک کاری و سوراخ کاری هستند که به تسریع فرآیند تولید کمک می کند.
محورهای اضافی برای تراشکاری پیچیده
در دنیای امروز تولید، محورهای اضافی مانند A، B و C در دستگاه های CNC به ویژه برای تراشکاری پیچیده بسیار حیاتی هستند. این محورهای چرخشی اجازه می دهند تا ابزار در زوایای مختلف حرکت کند و به تولید قطعاتی با هندسه های پیچیده و سطوح دقیق کمک کند. به عنوان مثال، با استفاده از دستگاه های ۴ محور و ۵ محور، تولیدکنندگان می توانند قطعات را در یک مرحله و بدون نیاز به تنظیمات متعدد تولید کنند که این امر به ویژه در صنایع حساس مانند هوافضا و خودروسازی اهمیت فراوانی دارد.
این محورهای اضافی به کاهش زمان تولید و افزایش کارایی کمک می کنند و به تولیدکنندگان این امکان را می دهند که به راحتی از طرح های پیچیده و خلاقانه پیروی کنند. همچنین، با کاهش نیاز به جابجایی و تنظیمات مکرر، خطر خطا و نقص در محصولات نهایی نیز به حداقل می رسد.
مزایای استفاده از چندین محور
استفاده از دستگاه های CNC چندمحوره، مزایای فراوانی را برای تولیدکنندگان به همراه دارد. برخی از این مزایا عبارتند از:
افزایش دقت: قابلیت کنترل دقیق در چندین محور، به تولید قطعات با دقت و کیفیت بالا کمک می کند.
کاهش زمان تولید: با انجام عملیات مختلف در یک مرحله، زمان مورد نیاز برای تولید کاهش می یابد.
کاهش هزینه ها: به دلیل کاهش زمان و منابع مورد نیاز، هزینه های تولید به طرز قابل توجهی کاهش می یابد.
انعطاف پذیری بالا: این دستگاه ها می توانند انواع مختلفی از مواد را پردازش کنند و امکان تولید قطعات متنوعی را فراهم می آورند.
به کارگیری چندین محور در دستگاه های CNC، به تولیدکنندگان این امکان را می دهد که در بازار رقابتی امروز، نوآوری های بیشتری در فرآیندهای تولید خود ایجاد کنند و به سطوح جدیدی از کیفیت و کارایی دست یابند.
تاثیر فناوری CNC در صنعت تولیدی
تکنولوژی CNC (کنترل عددی کامپیوتری) به طور چشمگیری نیاز به نیروی کار ماهر را در صنعت تولیدی کاهش داده است. با اتوماسیون فرآیندهای تولید، ماشین آلات CNC به طور خودکار وظایف پیچیده را انجام می دهند و این امر باعث می شود که کارگران با مهارت های پایین تر نیز قادر به بهره برداری از این ماشین آلات باشند.
به عنوان مثال، در گذشته تولید قطعات پیچیده نیازمند دانش فنی عمیق و تجربه زیادی بود. اما اکنون با استفاده از نرم افزارهای کاربری ساده و رابط های کاربری گرافیکی، اپراتورها می توانند به راحتی کدهای CNC را برنامه ریزی کنند و دستگاه ها را راه اندازی کنند. این تغییرات به تولیدکنندگان این امکان را می دهد که با کاهش هزینه های نیروی کار، به افزایش سودآوری بپردازند.
افزایش دقت و کیفیت قطعات
فناوری CNC به عنوان ابزاری کلیدی در افزایش دقت و کیفیت قطعات تولیدی شناخته می شود. این تکنولوژی به تولیدکنندگان اجازه می دهد که ابعاد و شکل های پیچیده را با حداقل خطا تولید کنند. به خصوص در صنایع حساس مانند هوافضا و پزشکی، دقت بالای تولید می تواند تأثیر بسزایی در عملکرد نهایی محصولات داشته باشد.
برخی از مزایای دقت و کیفیت در تولید با CNC عبارتند از:
– **دقت بالا**: ماشین آلات CNC قادرند تا ابعاد دقیق را با خطای کمتر از یک میلی متر تولید کنند.
– **تکرارپذیری**: تولید قطعات با کیفیت یکسان در هر بار تولید، که به ویژه در تولید انبوه اهمیت دارد.
– **کاهش ضایعات**: با دقت بالاتر، میزان مواد ضایع شده به طور چشمگیری کاهش می یابد.
این دقت و کیفیت بالای تولید نه تنها به افزایش رضایت مشتریان کمک می کند، بلکه اعتماد بیشتری را نسبت به برندهای تولیدکننده ایجاد می نماید.
بهبود بهره وری و کاهش هزینه ها
یکی از بزرگ ترین مزایای فناوری CNC، بهبود بهره وری و کاهش هزینه ها در فرآیندهای تولید است. با اتوماسیون و کاهش زمان تنظیمات، ماشین آلات CNC توانایی تولید سریع تر و مؤثرتر قطعات را دارند.
در شرایطی که نیاز به تولید انبوه و سریع محصولات با تنوع بالا وجود دارد، CNC به عنوان ابزاری کارآمد عمل می کند. برخی از تأثیرات مثبت این فناوری عبارتند از:
– **کاهش زمان تولید**: زمان لازم برای تنظیمات و تولید قطعات به طور قابل توجهی کاهش می یابد.
– **کاهش هزینه های عملیاتی**: با افزایش سرعت تولید، هزینه های مرتبط با نیروی کار و فرآیندها کاهش می یابد.
– **پاسخگویی به نیازهای بازار**: توانایی تولید سریع و با کیفیت بالا، تولیدکنندگان را قادر می سازد تا به سرعت به تغییرات بازار پاسخ دهند.
استفاده از فناوری CNC به تولیدکنندگان این امکان را می دهد که در رقابت با سایرین مزیت های قابل توجهی کسب کنند و در عین حال به بهبود کیفیت و کاهش هزینه ها بپردازند.